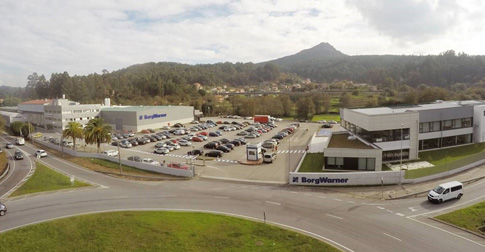
La solución viene del lado de la inteligencia artificial, la internet de las cosas y el Big Data que se combinan para ofrecer ambientes saludables y sostenibles, así como un mayor ahorro energético.
Veamos la experiencia del proveedor automotriz estadounidense Borgwarner, con sede en Vigo. La empresa necesitaba un sistema de gestión eficiente para integrar las diferentes tecnologías de las instalaciones en una herramienta única. ¿El objetivo? Mejorar el confort ambiental, disminuir los costes y el consumo de energía de la planta industrial y de las oficinas.
¿Cómo lo hicimos? Primero, logramos la monitorización y control del coste energético. Esto fue posible a través de la integración de la información de analizadores, sensores, SCADAs, ERPs, MES, MOM y otros sistemas en una solución adaptada al negocio y necesidades del cliente.
Después, diseñamos sistemas de recuperación de energía a medida para optimizar el consumo energético. Así, entre otras acciones, instalamos intercambiadores de aceite-agua en los compresores que abastecen de aire comprimido a las líneas de producción. Esto permite recuperar la energía disipada en forma de calor.
Finalmente, desarrollamos sistemas de refrigeración exprofeso que disminuyen el consumo eléctrico. Por ejemplo, integramos un aerorefrigerador en los hornos de producción que enfría el agua utilizando el aire del exterior.
Uno de los principales resultados ha sido la mejora de las condiciones del ambiente y la ventilación en el centro tecnológico de la empresa y la reducción del consumo de suministros. Las oficinas necesitaron un 20 por ciento menos de electricidad gracias al sistema de climatización abastecido con energía emanada del proceso productivo.
En cuanto al centro de fabricación, se optimizaron las instalaciones y su mantenimiento. También se consiguió un mayor control de la iluminación, la climatización, el compresor de aire y los combustibles. Además, se integraron el modo de emergencia y los automatismos para abaratar costes.
La incorporación de un panel único de monitorización del centro tecnológico y de la planta de fabricación facilita la gestión. Desde allí, se generan informes personalizados con datos y KPIs y se pueden recibir alertas para prevenir averías. Esto agiliza la toma de decisiones.
Las medidas de eficiencia implementadas elevaron la rentabilidad de las instalaciones en un 20 por ciento. Esto mejoró notablemente la competitividad de Borgwarner: la compañía incrementó su volumen de producción en un cinco por ciento respecto del año anterior sin aumentar su coste energético. Y todo esto con una estrategia de telegestión sostenible que contribuye a la descarbonización del sector industrial.